Allgemeines Projekt
Numerische Simulation der Rohrherstellung bestehend aus Walzprofilieren und Hochfrequenz-Induktionsschweissen
Das Institut für Computational Engineering ICE (OST) hat ein vollständig gekoppeltes dreidimensionales Finite-Elemente-Modell für die Simulation eines Rohrherstellungsprozesses entwickelt, der aus Walzprofilieren und Hochfrequenz-Induktionsschweißen besteht. Auf der Grundlage des validierten Finite-Elemente-Modells können die komplexen physikalischen Wechselwirkungen beim HFI-Schweissen und der Einfluss der Fertigungsparameter systematisch untersucht werden. Dies wird dazu beitragen, den HFI-Schweissprozess im Hinblick auf die Verarbeitung von Stählen mit einem hohen Kohlenstoffäquivalent und hohen Festigkeiten zu verbessern.
Längsnahtgeschweisste Rohre – Herstellung, Anwendung und Herausforderung
Derzeit werden etwa 70 % der Stahlrohre mit einem Durchmesser kleiner als 300 mm als längsnahtgeschweisste Rohre hergestellt. Bei der Herstellung von längsnahtgeschweissten Rohren wird ein Stahlband durch Walzprofilieren zu einem Rohr mit offener Naht, einem sogenannten Schlitzrohr geformt. Anschliessend wird der verbleibende Spalt durch Schweissen geschlossen. Das gebräuchlichste Schweissverfahren ist das Hochfrequenz-Induktionsschweissen (HFI).
Längsnahtgeschweisste Rohre aus hochfestem Stahl werden heutzutage häufig in der Automobilindustrie eingesetzt um das Gewicht und dadurch den Kraftstoffverbrauch von Autos zu reduzieren. Die dafür verwendeten Stähle mit einem relativ hohen Kohlenstoff- und Mangangehalt zeichnen sich durch eine gute Härtbarkeit und hohe Festigkeit aus, lassen sich aber nur schwierig schweißen. Um solche Stahlsorten zuverlässig verarbeiten zu können, muss der Schweißprozess optimiert werden.
Warum wird eine numerische Simulation der Rohrherstellung benötigt?
Aktuell werden die zum Walzprofilieren und HFI-Schweissen eingesetzten Werkzeuge, Verfahren und Prozessparameter überwiegend empirisch ausgelegt. Bei komplexen Verfahren wie dem HFI-Schweissen von Rohren ist diese auf Versuch und Irrtum basierende Prozessauslegung häufig nicht zielführend. Um die steigenden Marktanforderungen hinsichtlich dem Werkstoff mit immer höheren Festigkeiten und höherem Legierungsanteil, der Schweissnahtqualität sowie dem Kostendruck meistern zu können werden andere Methoden zur Prozessoptimierung benötigt. Eine hierfür bestens geeignete und etablierte Technik ist die Finite-Elemente-Methode (FEM).
Das Walzprofilieren und HFI-Schweissen von längsnahtgeschweissten Rohren wurde bisher bereits in mehreren wissenschaftlichen Arbeiten basierend auf FE-Simulationen untersucht [1-5]. Jedoch berücksichtigt keine dieser Schweißsimulation die exakte Geometrie der Fügeflächen und die Eigenspannungen innerhalb des Stahlbandes, die beim Walzprofilieren entstehen. Außerdem wurde in allen genannten Veröffentlichungen die Bewegung des Rohres sowie die Phasenumwandlungen innerhalb des Werkstoffs aufgrund von Temperaturänderungen vernachlässigt.
Entwicklung eines validierten Prozessmodells
In diesem Projekt wurde ein dreidimensionales FE-Modell für eine gekoppelte elektromagnetisch-thermisch-mechanische Simulation des Rohrherstellungsprozesses, bestehend aus Walzprofilieren und HFI-Schweißen entwickelt. Im Vergleich zu anderen Arbeiten berücksichtigt die Schweißsimulation
- die exakte Geometrie des Schlitzrohrs,
- die beim Walzprofilieren erzeugten Eigenspannungen,
- die Bewegung des Rohrs,
- die durch Temperaturänderungen verursachten Phasenumwandlungen im Werkstoff.
Für die Simulation des HFI-Schweißprozesses wurde die Dual-Mesh-Methode verwendet. Die Fliesskurve, die thermischen, mechanischen, elektrischen und magnetischen Eigenschaften wurden experimentell ermittelt und in Abhängigkeit der Temperatur und Phase modelliert. Die Zeit-Temperatur-Umwandlungsdiagramme für die Phasenumwandlung beim Aufwärmen und Abkühlen wurden teilweise experimentell ermittelt oder auf der Grundlage der chemischen Zusammensetzung des Stahls berechnet.
Die experimentelle Validierung der Simulationsergebnisse zeigt, dass die Geometrie des Schlitzrohrs, die Geometrie des geschweissten Rohrs, die Kräfte auf die Stauchrollen, die Temperatur entlang der Fügefläche, die Sanduhrform der martensitischen Schweissnaht und die Härteverteilung innerhalb der Wärmeeinflusszone mit Hilfe der FEM vorhergesagt werden können [6].
Quellen:
[1] Das, P.; Asperheim, J. I.; Grande, B. et al.: Three-dimensional numerical study of heat-affected zone in induction welding of tubes. COMPEL - The international journal for computation and mathematics in electrical and electronic engineering. 39 (2020), S. 213–219 (DOI: 10.1108/COMPEL-06-2019-0238)
[2] Ebel, W.; Kroll, M.; Nikanorov, A. et al.: Numerical simulation of inductive longitudinal HF welding of cladded pipes. Vulkan-Verlag GmbH (2019), S. 43–51.
[3] Ghaffarpour, M.; Akbari, D.; Moslemi Naeeni, H. et al.: Improvement of the joint quality in the high-frequency induction welding of pipes by edge modification. Welding in the World. 63 (2019), S. 1561–1572. (DOI: 10.1007/s40194-019-00779-0)
[4] Han, Y.; Xiao, Y.; Yu, E. - L. et al.: Electromagnetic heating and motion mechanism for contact welded pipes based on a node sequential number method. Applied Thermal Engineering. 137 (2018), S. 822–835. (DOI: 10.1016/j.applthermaleng.2018.03.101)
[5] Kang, C.; Shi, C.; Liu, Z. et al.: Research on the optimization of welding parameters in high-f requency induction welding pipeline. Journal of Manufacturing Processes. 59 (2020), S. 772–790. (DOI: 10.1016/j.jmapro.2020.10.021)
[6] Egger, C.; Lüchinger, M.; Schreiner, M. et al.: Numerical Simulation of Tube Manufacturing Consisting of Roll Forming and High-Frequency Induction Welding. Materials. 15 (2022) (DOI: doi.org/10.3390/ma15031270)
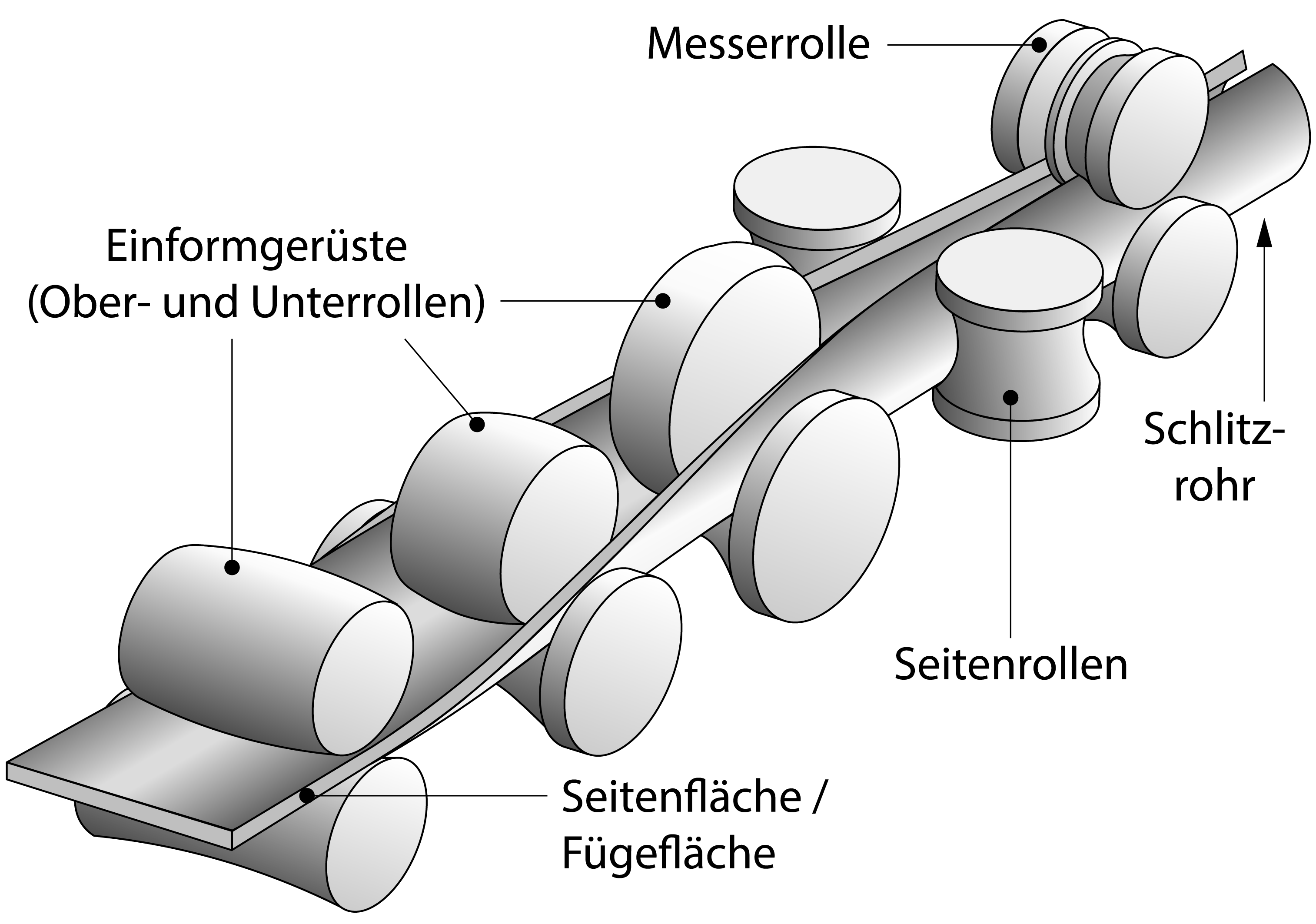
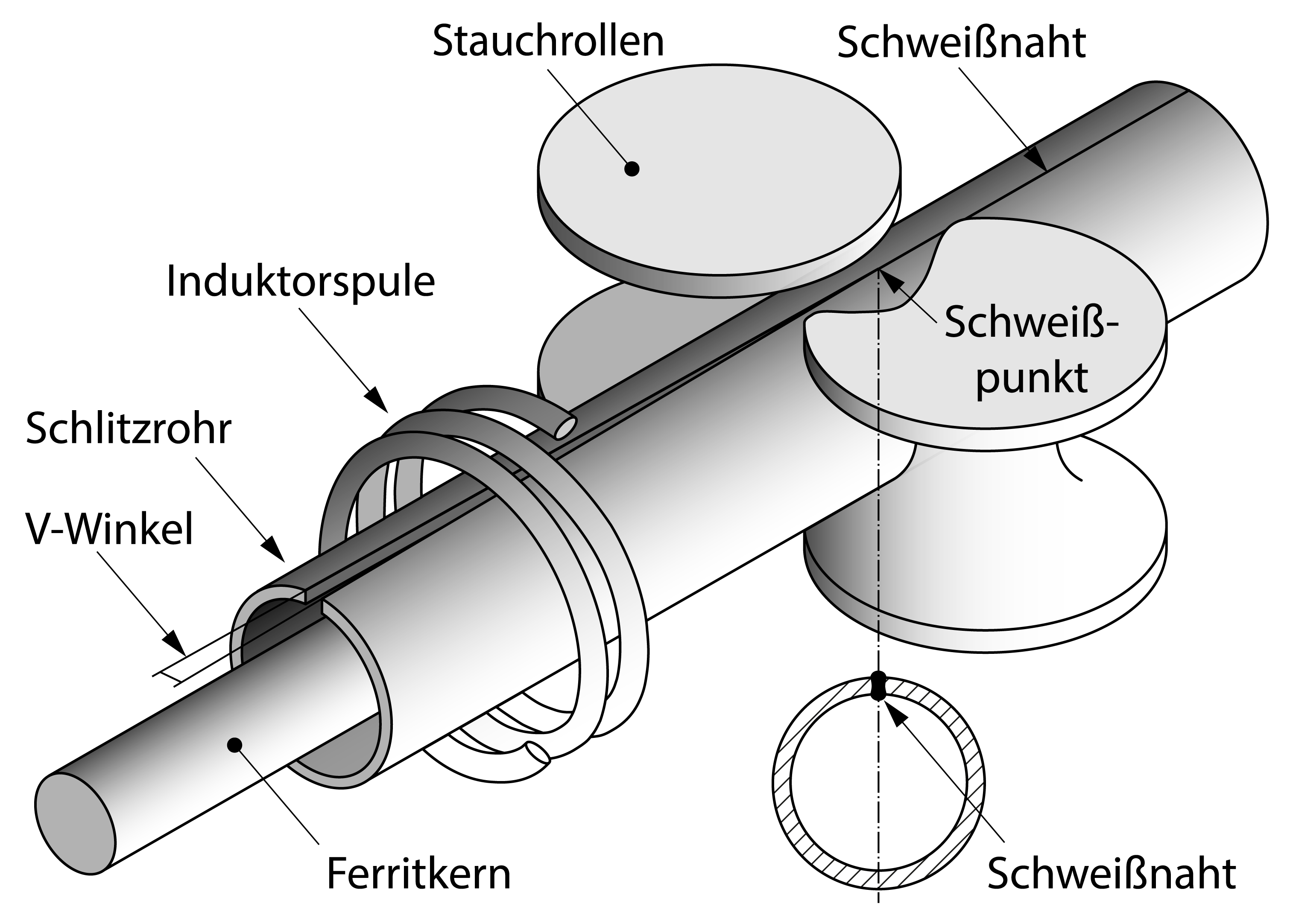

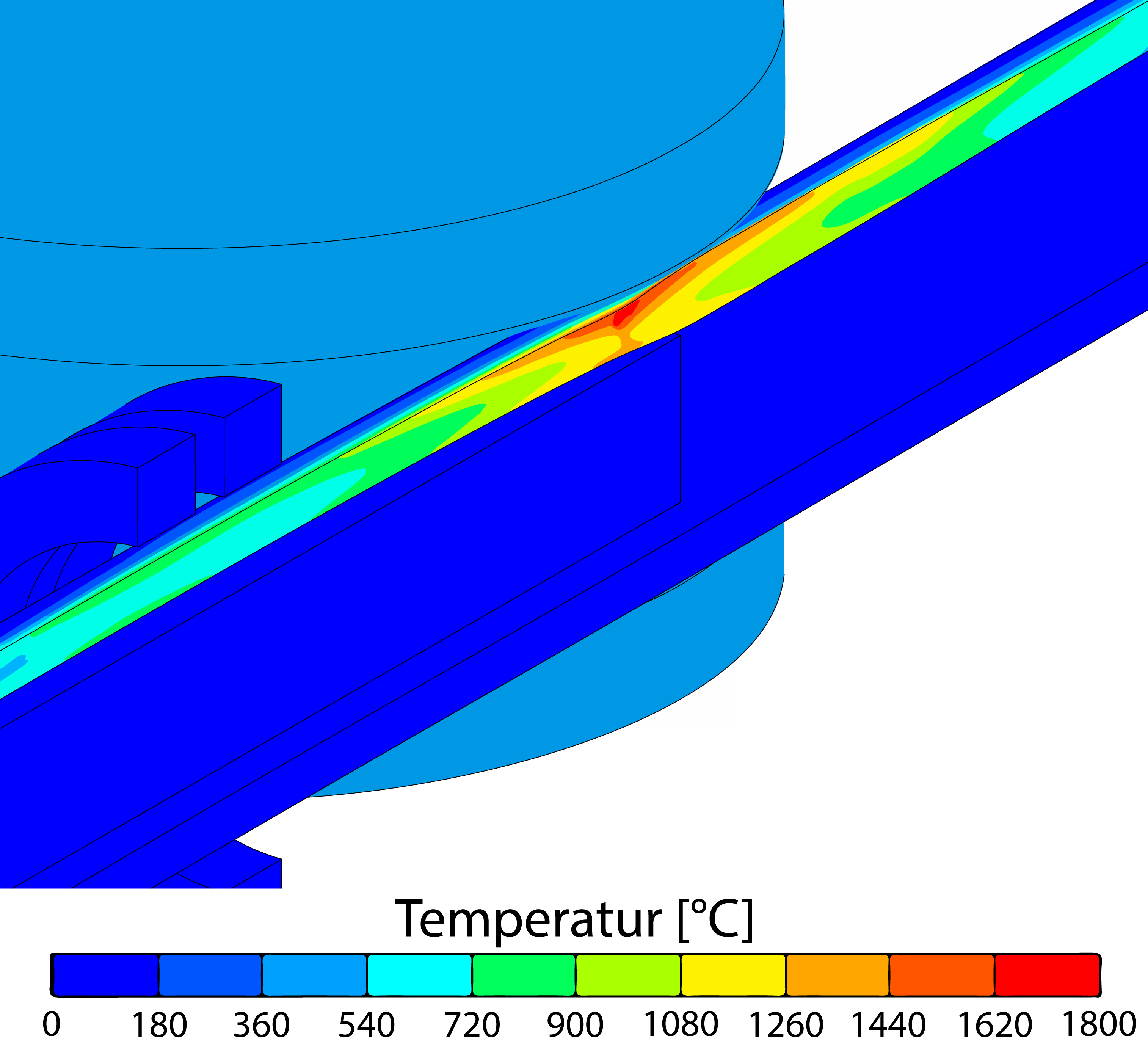
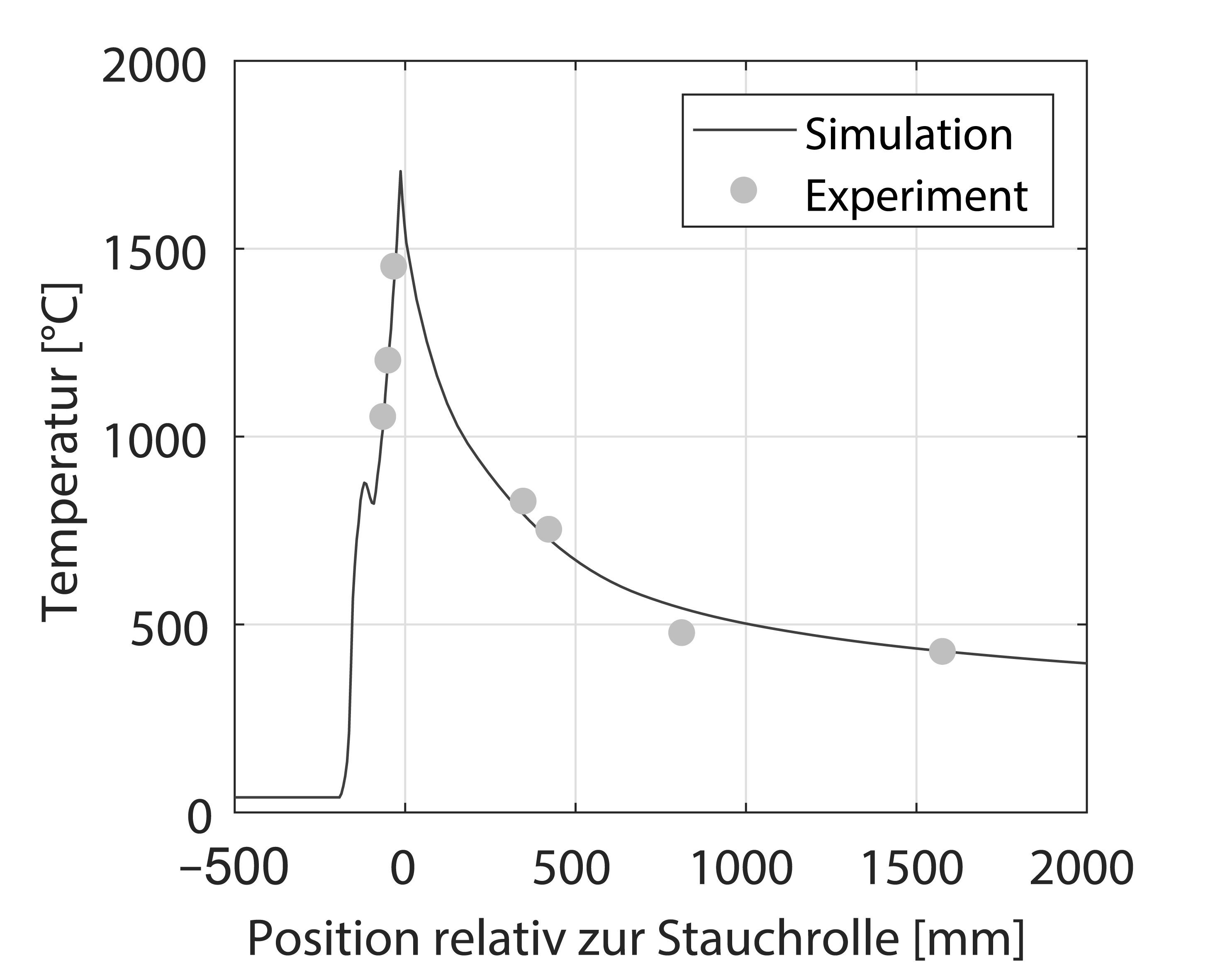

Laufzeit: 01.10.2018 - 31.12.2021
Projektteam:
Prof. Dr. Michael Schreiner
Studiengang BSc SystemtechnikLehrbeauftragter für Angewandte Mathematik
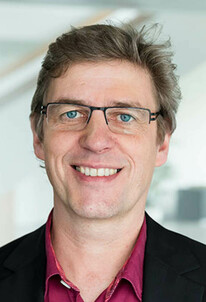
Dr. Marco Lüchinger
ICE Institut für Computational EngineeringSenior Research Engineer
+41 58 257 33 82marco.luechinger@ost.ch
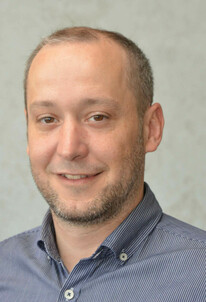
Christian Johannes Egger
ICE Institut für Computational EngineeringWissenschaftlicher Mitarbeiter
+41 58 257 33 49christian.egger@ost.ch
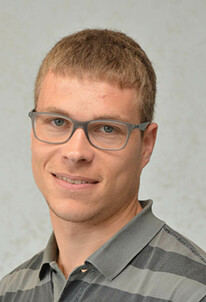