Forschungsprojekt
Mikrostrukturierte thermoelektrische Generatoren
Thermoelektrische Generatoren (TEG) wandeln Wärme in elektrische Energie um. Sie werden zum Beispiel als Energiequellen für Sensoren an schwer zugänglichen Orten eingesetzt.
Mit TRW Switzerland als Projektpartner wurde ein 24-monatiges KTI-Projekt erfolgreich durchgeführt. Das Ziel war, einen industrietauglichen Fabrikationsprozess für thermoelektrische Generatoren (TEG) zu entwickeln.
Aufbau eines TEGs
Ein TEG besteht aus vielen Thermoelementen, welche in Serie geschaltet sind. Dafür werden elektrisch leitfähige Materialien benötigt, die als Paar einen möglichst hohen thermoelektrischen Effekt aufweisen. Hier kommen unterschiedliche Metalle oder besser noch Halbleitermaterialien in Frage. Diese werden in eine Matrix eingebettet. Für einen TEG sollten dafür einfach strukturierbare Materialien mit niedrigen Wärmeleitkoeffizienten verwendet werden. Im Rahmen bisheriger Untersuchungen entschied man sich für SU8, FR4 und Polyimid.
Kennwerte
- Substratdicke: 0.2 – 0.51 mm
- Substratgrösse: bis 4“ quadratisch
- Anzahl Thermoelemente: bis zu 1300
- Tmax: 200 °C
- Pmax: 1000 µW
Projektdetails
Um einen TEG kostengünstig herzustellen, wird ein grossflächiges Substrat (Matrix) mit Löchern benötigt. Die Löcher werden anschliessend mit zwei verschiedenen Materialien (zum Beispiel Kupfer und Nickel) galvanisch gefüllt. Diese so hergestellten metallischen Schenkel werden jeweils miteinander verbunden, einzelne seriell verschaltete Thermoelemente entstehen. Je nach Einsatzgebiet muss der TEG anschliessend verkapselt werden.
Es wurden verschiedene Matrixmaterialien eruiert und getestet. Dabei waren einerseits die physikalischen Eigenschaften (Wärmeleitfähigkeit, Ausdehnungskoeffizient, …), andererseits die Kosten, die Verfügbarkeit und die Möglichkeit, das Material gut zu bearbeiten, wichtig. Schlussendlich wurden FR4 und Polyimid verwendet. Die Löcher für die Schenkel werden mittels konventionellen Bohrens bereitgestellt.
Als Füllmaterialien für Löcher wurde im ersten Schritt Kupfer und Nickel verwendet, da diese Materialien gut galvanisch abscheidbar sind. So konnte ein industrialisierbarer Herstellungsprozess definiert werden. Ein Fokus bei der Entwicklung des Prozesses war die Skalierbarkeit für eine zukünftige Massenfertigung. Mittelfristig müssen zur Steigerung des Wirkungsgrades der TEGs effizientere Materialpaarungen eingesetzt werden.
Verschiedene Packagingvarianten wurden ausgetestet. Ein Material ist dann gut geeignet, wenn es möglichst resistent gegenüber Umwelteinflüssen ist und eine hohe Wärmeleitfähigkeit aufweist. Lötstopplack, silikonbasierte Vergussmasse und plasmagespritztes Bornitrid lieferten dünne, stabile Schichten und kapseln den TEG gut gegen die Umwelt ab. In Anlehnung an herkömmliche Peltierelemente wurden auch Aluminiumnitrid-, Aluminiumoxid- und Aluminiumplättchen aufgelötet. Diese Materialien zeichnen sich durch eine gewünschte hohe Wärmeleitfähigkeit aus, sind aber in puncto Temperaturwechselbeständigkeit als starr und spröde einzuordnen.
Projektpartner
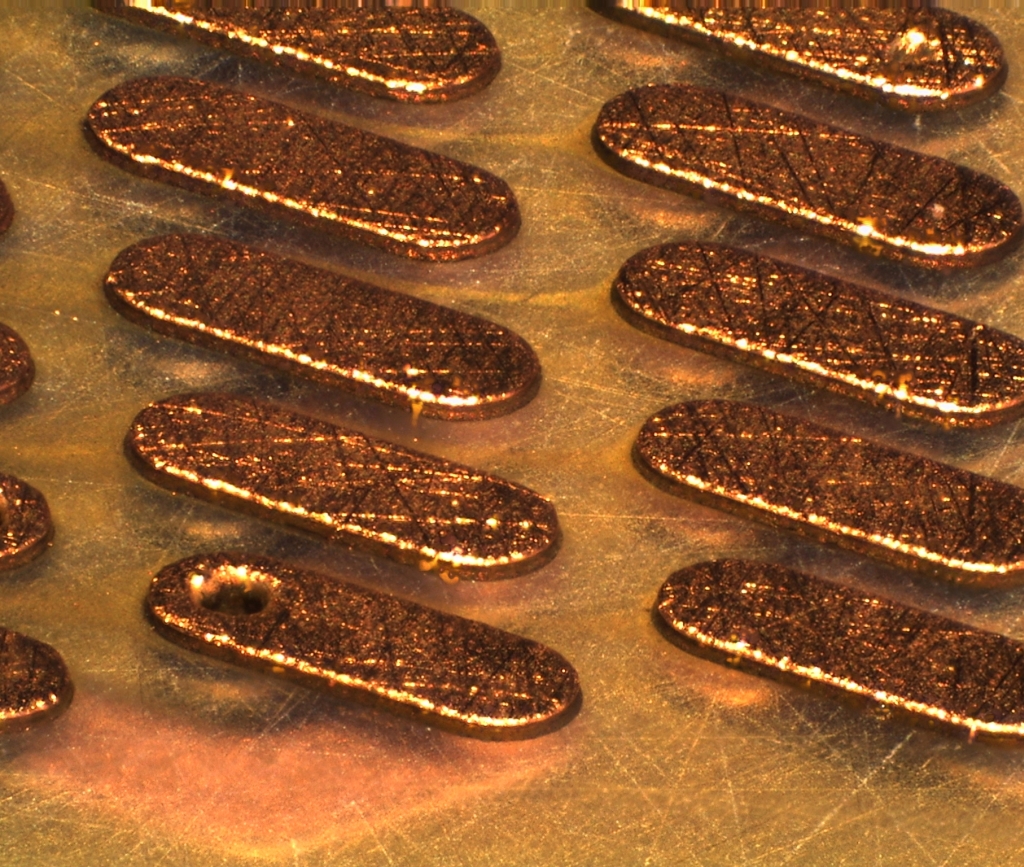


Laufzeit: 14.07.2016
Projektteam:
Prof. Dr. Martin Gutsche
IMP Institut für Mikrotechnik und PhotonikProfessor für Mikrotechnik, Leiter Kompetenzbereich Prozesstechnologie
+41 58 257 34 68martin.gutsche@ost.ch
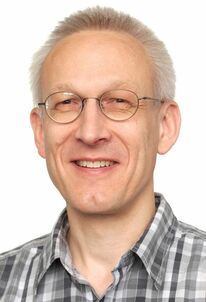
Marco Cucinelli
IMP Institut für Mikrotechnik und PhotonikLeiter Reinraum
+41 58 257 34 57marco.cucinelli@ost.ch
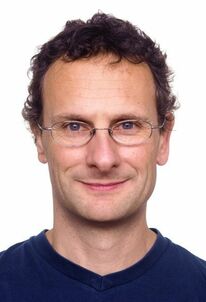