Research project
COPlasma - using a plasma reactor to reduce CO2 emissions in industry
Our research team is pursuing the approach of directly reusing CO2 emissions from energy-hungry industries, such as the cement industry, to generate energy. This saves money and causes fewer climate-damaging emissions. To this end, a new type of plasma reactor has been developed that uses waste gases as a recycled fuel and generates energy from them.
Increasing prices on the global market and the fear of supply bottlenecks pose major challenges for industrial production facilities. Problems could arise in the future, particularly where large quantities of thermal energy are required. The cement industry, for example, is one of the industries with an extremely high demand worldwide. This is mainly met by burning waste and fossil fuels such as gas or oil. However, the absence of fossil fuel supplies or their reduction cannot be compensated for so easily. With up to 30% of the combustion mixture, they are required as a standard fuel for constant production operations. Another challenge is the reduction of CO2 emissions. The CO2 is produced both during the production of the cement clinker and during the combustion of the fuels.
Funded by the Swiss Federal Office of Energy (SFOE), UMTEC has been working feverishly on a radically new and innovative solution. The result is now impressive: A specially developed plasma reactor that uses cold plasma technology to generate sustainable fuel from electricity.
Radically different
In the truest sense of the word. Instead of a traditional heat-driven process, the plasma reactor uses high electric fields to break down molecules and atoms into their components. This makes it possible to move the inert CO2 molecule to a conversion using only an electric current. Heat losses are thus avoided and process efficiency is increased. The mechanisms involved are mostly radical.
Two flies with one flap
The advantage of the plasma solution lies not only in the infinitely variable and delay-free provision of a CO/O2 fuel mixture at the touch of a button, but also in the quantities of climate-damaging CO2 that are saved and not emitted. The actual waste product of clinker production, CO2, thus becomes a reusable and valuable energy source - “two birds with one stone”, so to speak.
Good turnover and high energy efficiency
With a turnover of approx. 30% and an energy efficiency of almost 60% (plasma power to fuel oxidation), plasma technology is already on a par with current power-to-X technologies, such as the production of hydrogen by means of electrolysis or the production of artificial fuels via catalytic CO2 conversion.
Excellent
The Foundation for the Promotion and Support of Technology-oriented Enterprises Rapperswil (FUTUR Foundation for short) awarded the main prize to the research project and its successes on June 16, 2022. The project has thus been honored!
Further development potential
The electricity costs of fuel production are currently estimated at a good CHF 120/MWh. It therefore costs around CHF 200 to convert one ton of CO2 into fuel. Although these are already excellent figures, there is still room for improvement. In further work, innovative material solutions should make it possible to increase sales, increase efficiency and reduce production costs.
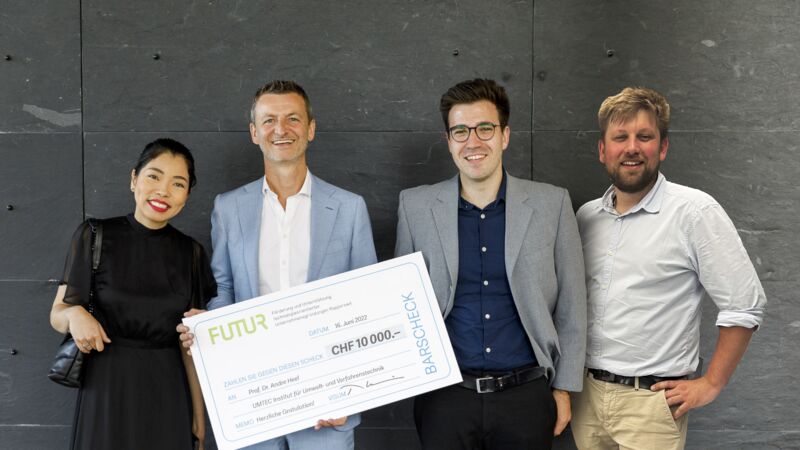
Team:
Dr. Bastian Welte
UMTEC Institut für Umwelt- und VerfahrenstechnikProjektleiter
+41 58 257 43 91bastian.welte@ost.ch
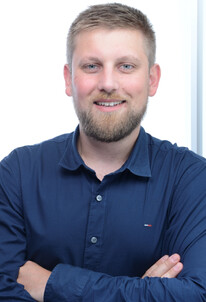
Prof. Dr. Andre Heel
UMTEC Institut für Umwelt- und VerfahrenstechnikProfessor, UMTEC
+41 58 257 43 87andre.heel@ost.ch
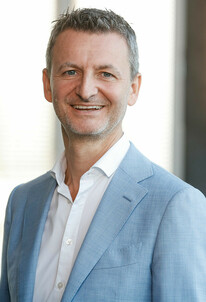