Research project
Collaborative Robotics (CoBot)
We support companies in the evaluation and implementation of collaborative robotics solutions. Our competences include the design of automated robotic systems, simulation and programming of collaborative robots (CoBots) as well as image processing and human-machine interface.
Collaborative Robots (CoBots) are able to redefine the possibilities for industrial robotics: These robots have sensitive sensors or compliance to enable close human-robot cooperation.
The expertise of the ILT includes:
• robotic cell design
• robot simulation and programming of CoBots
• vision and human machine interface
The ILT assists companies in evaluating robotic technologies and
implementing collaborative robotic solutions. We are looking forward
to supporting you!
We offer an continuing education on "collaborative robotics in practise". Further information here
VIDEO zu Collaborative Robotics: LBR iiwa implemented by ILT
Interview mit Agathe Koller zur kollaborativen Robotik: Technische Rundschau 07/17
The ILT has completed the following projects:
Collaborative assembly cell
For the future assembly workplace, a collaborative assembly cell was developed for Phoenix Mecano. In this cell, humans and robots assemble an electrical cylinder in close collaboration. The production worker and the robot are allowed to work hand in hand. Both the processes and the hardware were realised by Phoenix Mecano, whereas the ILT optimizied the peripheral interfaces of the robot and its path planning. Theresult is a significantly increased process safety.
Demonstration cell with the LBR iiwa
The demonstration cell is used to present the potential of collaborative robotics to a wider audience in exhibitions. The main aspects of the demonstration cell are:
- flexible way to automate manual processes in laboratories
- direct and safe interaction between robot and production worker
- space-saving implementation (because protective fences are no longer required)
- interface possiblities like SiLA® for integration in subordinate control systems
Collaborative HRC bin picking in the box
On behalf of thyssenkrupp Presta, a master thesis has been written on the "collaborative HRC bin picking in the box". A repetitive and physically exhausting assembly step is performed by the LBR iiwa. Although there are restrictions regarding the speed, it could be shown that the collaborative bin picking in the box in the industrial setting is a resolvable task.
Automated charge verification
In close collaboration with a medical technology company, an automated charge verification in the production process was developed and realised with YuMi. Due to its collaborative qualities, this robotic system can be implemented in close proximity of production workers. Using the ABB simulation software, the whole path of motion of the YuMi was programmed and tested before the implementation of the system. This approach made it possible to identify critical aspects and take adequate actions.
Zum Projektbericht in der Technischen Rundschau
Intelligent card sorting with YuMi
During the automated extraction of large amounts of blood samples in the DBS device, carrier cards are usually manually sorted into the racks of the DBS. The ILT has realised an intelligent card sorting using a YuMi robot. YuMi recognises the orientation and position of the cards thanks to the integrated image processing system and the collision detection. This ensures that the cards are not picked in the sample field and that they are sorted correctly. Thanks to the integrated sensor technology, an efficient and quick implementation of current pick&place applications is possible with YuMi.
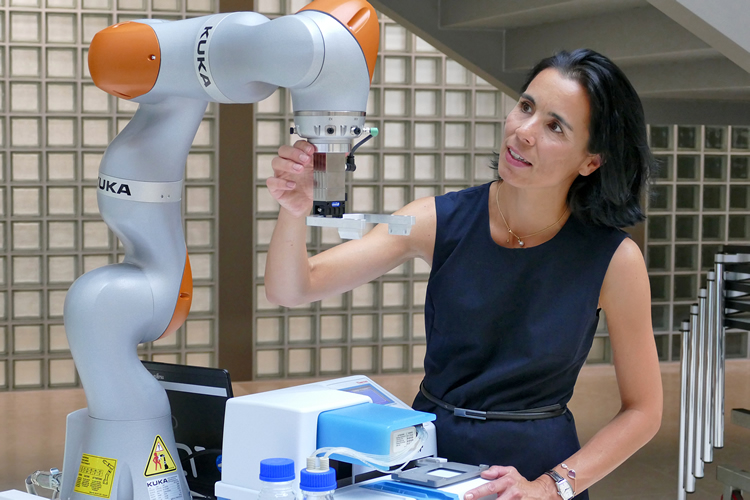
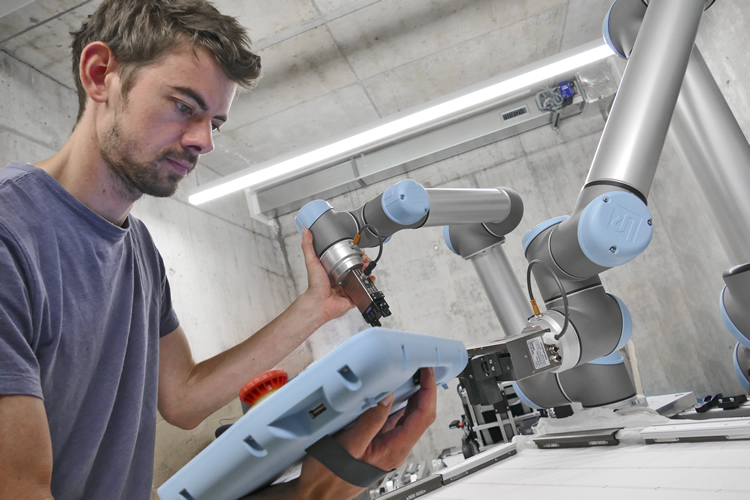

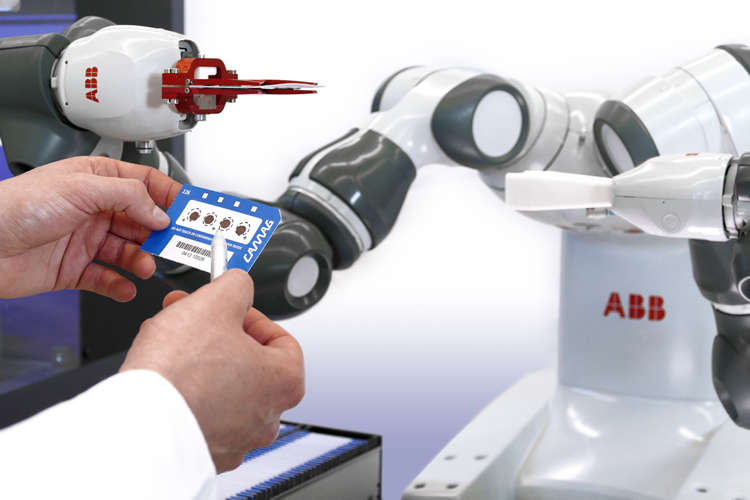
Project manager
Prof. Dr. Agathe Koller
ILT Institut für Laborautomation und MechatronikInstitutsleiterin ILT, Studiengangleiterin Master of Science MSE, Professorin
+41 58 257 49 29agathe.koller@ost.ch
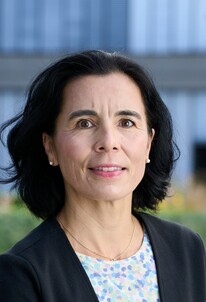